Design & Engineering
- Home
- Service
- Design & Engineering
Our Service
Service List
- Design & Engineering
- Precision Dies
- Die Assembly & Die Tryout
- Precision Parts
- Tooling&Jigs
Need For Some Help ?
For More Details Contact Us!
Phone
+86 0769-82759388-825 +86 0769-81502216-826
info@cymjkj.com
General Process of Design & Engineering
At Chaoyang Company, we integrate innovative design, advanced engineering, and meticulous craftsmanship to deliver precision metal stamping dies that exceed industry standards. From initial concept to final production validation, our full-service approach ensures your metal components achieve unmatched accuracy, durability, and cost-efficiency.
Design Optimization
Collaborative CAD modeling and DFM analysis to refine part geometry and tolerances.
Precision Tooling
High-accuracy progressive stamping dies engineered for demanding production needs
Rapid Prototyping
Soft tooling and quick sampling to validate form, fit, and function early.
in-House Testing
On-press die testing and processvalidation to ensure readiness formass production.
Specific solutions
There are different die solutions for the automotive, aerospace and electronics fields.
Lifetime support
Ongoing tooling maintenance.upgrades, and production scaling support
1. Collaborative Product Design & Optimization Services
Our experienced team of engineers uses a collaborative Design for Manufacturing (DFM) approach to consider the production process in advance during the product design phase to ensure that part structure, material, size, tolerance, etc., are suitable for mass manufacturing, reducing unnecessary complexity and avoiding production challenges, waste and high costs.
Using 3D modelling and simulation tools (including UG, PRO-E, CAD, CAE and CAM), we can identify potential formability issues early in the design process.
At the same time, our expertise in micro-precision manufacturing enables us to provide solutions for the development of ultra-thin components and complex micro-features such as connector pins, IC lead frames and EMI shielding parts.
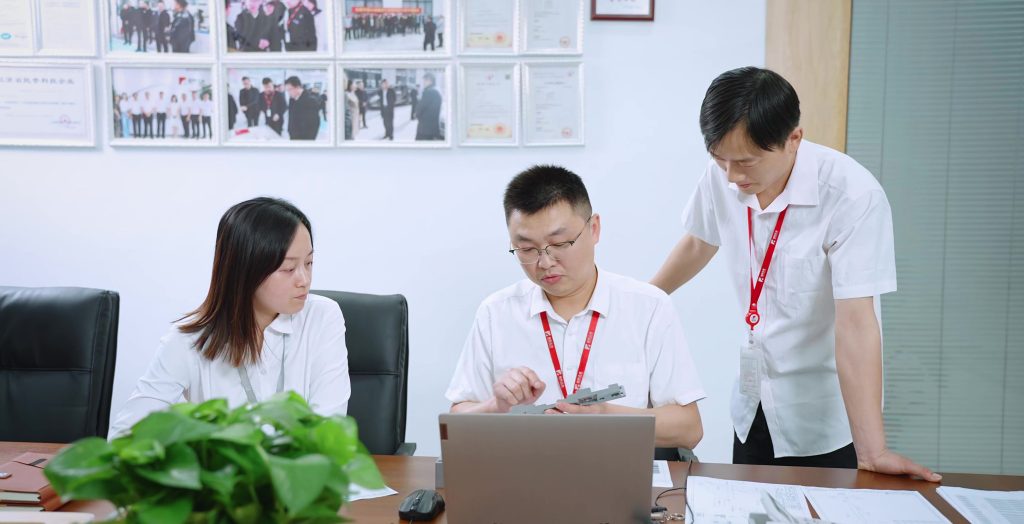
2. Precision Die Engineering & Tooling Development Core Capabilities
We specialise in precision die engineering and die development, with core capabilities covering the entire stamping process. Our progressive stamping die design process can handle complex processes, such as blanking, punching, bending, and deep drawing, in a single high-speed stamping operation using multi-stage tool configurations.
To ensure unparalleled precision, we use advanced machining techniques, including JG, PG, CNC milling, wire cutting and precision surface grinding, which can typically achieve precision tolerances of up to ±1μm for punches, dies and guide systems. In addition, we also utilise professional surface treatment technologies, such as TiCN and DLC coatings, as well as mirror polishing technology, to enhance the performance and service life of the dies, thereby achieving an excellent part surface finish.
At the same time, we can optimise dies for stainless steel, copper alloys, high-carbon steel, and special metals (such as titanium and Inconel).
3. Rapid Prototyping & Sample Validation Accelerate Time-to-Market
We use soft tooling, typically made of aluminum or pre-hardened steel, to produce functional prototypes for comprehensive design verification and performance testing. Our short-term stamping tests help confirm dimensional accuracy, material properties and assembly compatibility before full production. Rapid prototyping and sample verification can shorten your product’s time to market.
Based on actual test results, we make agile improvements to tooling designs to ensure optimal performance. This approach minimises expensive design modifications during mass production and is particularly useful for industries with strict certification requirements such as automotive, aerospace and medical.
4. Die Testing & Process Validation Rigorous Quality Assurance
We ensure rigorous quality assurance through comprehensive die testing and process validation. In-house stamping trials are performed using high-tonnage presses, allowing us to fine-tune critical parameters such as tonnage, feed speed, and lubrication for optimal performance.
Our advanced metrology and inspection tools—including CMMs, optical comparators, and surface roughness testers—verify that every die meets the most demanding customer specifications. Detailed performance reports are provided, covering tool life projections, maintenance schedules, and part consistency.
This meticulous process guarantees that every die we deliver is fully production-ready and capable of achieving zero-defect manufacturing at scale.
5. Industry-Specific Engineering Solutions Tailored for Your Sector
We offer industry-specific engineering solutions tailored to meet the unique demands of your sector. In the automotive and EV industries, we specialise in dies for motor laminations, battery contacts, sensor housings, and connectors—all designed to meet IATF 16949 quality standards.
For the electronics and 5G sectors, we deliver precision micro-dies used in high-frequency connectors, EMI shielding components, and ultra-miniaturised lead frames. In aerospace and defence, our lightweight tooling solutions utilise titanium and aluminium alloys, fully compliant with AS9100 and NADCAP certifications.
We also support the consumer goods industry with high-volume dies for appliances, wearables, and precision hardware, ensuring consistent quality and production efficiency at scale.
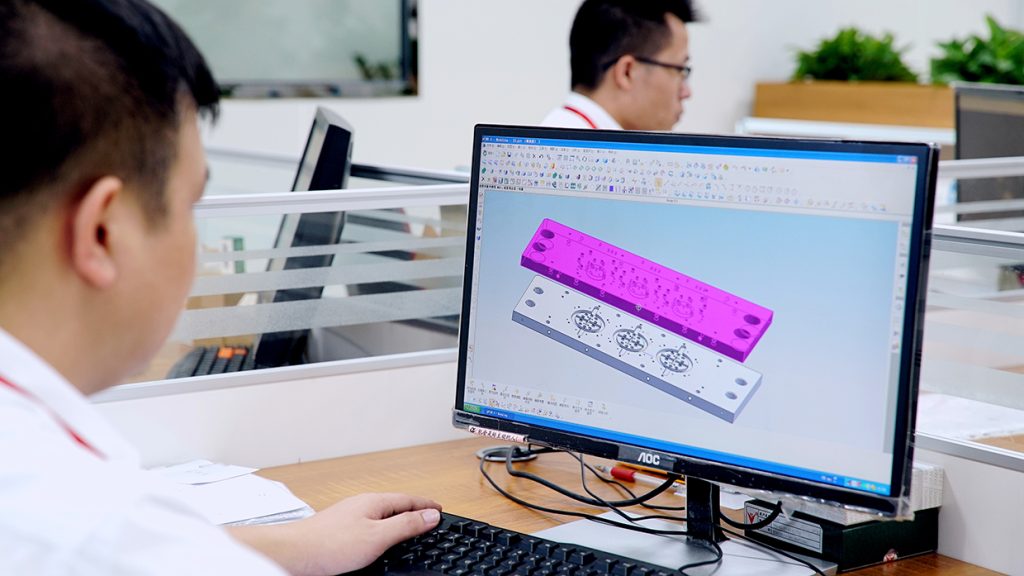
6. Lifetime Technical Support Beyond Delivery
Our commitment to your dies goes beyond delivery. We provide lifetime technical support to help you scale up production while maintaining the highest standards of precision and accuracy. Our team also offers comprehensive mould maintenance and refurbishment services, including regrind, component replacement, and recoating to extend the life of the mould.
In addition, we actively support the continuous improvement of products after they are launched, whether you want to reduce costs, improve product performance, or adapt to new production requirements.
Why Choose Us?
End-to-End Ownership: A single team manages design, engineering, and validation, ensuring seamless communication.
Cutting-Edge Infrastructure: JG, PG, Wire-EDM, CNC, Surface Grinder, high-speed stamping presses, and ISO-certified QA labs.
Proven Expertise: Decades of experience serving automotive, aerospace, electronics, and medical industries.
From Concept to High-Performance Production–
Partner with Chaoyang Company to transform your metal stamping challenges into competitive advantages. Contact us today to discuss your project’s unique requirements.
Make An Appointment
Pellentesque scelerisque auctor scelerisque.
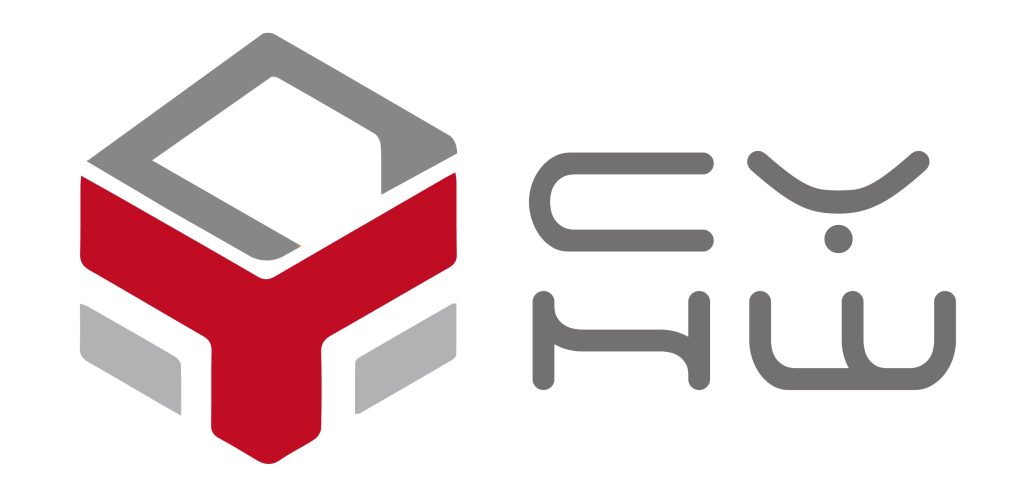
© 2025 Technical Support By LEZHAN